Manufacturing of Paper
Optimizing the Paper Manufacturing Process: Strategies for Cost Reduction and Efficiency
The manufacturing of paper typically involves several stages, including preparation of raw materials, pulping, papermaking, and finishing. Here's a general overview of the paper manufacturing process:
Raw Material Preparation: The primary raw material used for paper production is wood pulp, which can be obtained from different sources such as trees, recycled paper, or agricultural fibers like bamboo or bagasse. The raw materials are collected, sorted, and prepared for further processing.
Pulping: In this stage, the raw materials are processed to separate the cellulose fibers from other impurities. There are two primary pulping methods:
a. Mechanical Pulping: Involves grinding the raw material to separate the fibers mechanically. This method retains a higher percentage of the lignin present in the wood, resulting in a stronger paper but with lower brightness.
b. Chemical Pulping: Involves treating the raw material with chemicals to break down the lignin and separate the fibers. The two main chemical pulping methods are:
Kraft Pulping: Uses a combination of sodium hydroxide (NaOH) and sodium sulfide (Na2S) to dissolve the lignin.
Sulfite Pulping: Utilizes sulfurous acid (H2SO3) or bisulfites to remove lignin.
Chemical pulping results in higher-quality paper with better brightness, but it requires additional chemical processing and is more expensive than mechanical pulping.
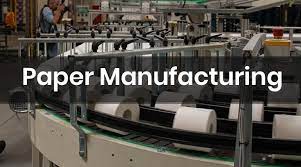
Papermaking: a. Beating: The fibers obtained from pulping are mixed with water and beaten to improve their bonding ability. This process helps create a uniform suspension of fibers called pulp.
b. Formation: The pulp is poured onto a moving mesh screen, known as the paper machine wire, which allows the water to drain while retaining the fibers in the desired pattern and thickness. The remaining water content is further removed using mechanical pressing and vacuum systems.
c. Drying: The wet paper sheet is then passed through heated rollers or a drying section to evaporate the remaining water and increase its strength.
Finishing:
a. Sizing: The paper may undergo sizing, a process where starch or other chemicals are applied to improve its surface properties, such as water resistance and printability.
b. Coating: Some types of paper, like glossy or coated paper, receive an additional coating layer to enhance smoothness, brightness, and ink absorption.
c. Calendering: The paper can be passed through a set of heated rollers, called a calender, to further enhance its smoothness, gloss, and thickness.
d. Cutting and Reeling: The large paper rolls are cut into smaller rolls or sheets of desired dimensions and then wrapped for storage or transportation.
It's important to note that there are variations in the paper manufacturing process depending on factors like the type of paper being produced (e.g., newsprint, fine paper, tissue paper) and the specific machinery and technologies used by different paper mills.
Visit: https://bestpaperaward.blogspot.com/
#PaperManufacturing
#PulpAndPaper
#PaperProduction
#SustainablePaper
#GreenPaper
#PaperIndustry
#Papermaking
#InnovationInPaper
#EfficientPaper
#RecycledPaper
Facebook: https://www.facebook.com/profile.phpid=100087106114908
The manufacturing of paper typically involves several stages, including preparation of raw materials, pulping, papermaking, and finishing. Here's a general overview of the paper manufacturing process:
Raw Material Preparation: The primary raw material used for paper production is wood pulp, which can be obtained from different sources such as trees, recycled paper, or agricultural fibers like bamboo or bagasse. The raw materials are collected, sorted, and prepared for further processing.
Pulping: In this stage, the raw materials are processed to separate the cellulose fibers from other impurities. There are two primary pulping methods:
a. Mechanical Pulping: Involves grinding the raw material to separate the fibers mechanically. This method retains a higher percentage of the lignin present in the wood, resulting in a stronger paper but with lower brightness.
b. Chemical Pulping: Involves treating the raw material with chemicals to break down the lignin and separate the fibers. The two main chemical pulping methods are:
Kraft Pulping: Uses a combination of sodium hydroxide (NaOH) and sodium sulfide (Na2S) to dissolve the lignin.
Sulfite Pulping: Utilizes sulfurous acid (H2SO3) or bisulfites to remove lignin.
Chemical pulping results in higher-quality paper with better brightness, but it requires additional chemical processing and is more expensive than mechanical pulping.
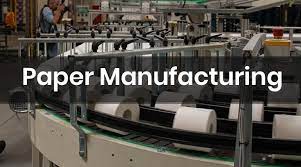
Papermaking: a. Beating: The fibers obtained from pulping are mixed with water and beaten to improve their bonding ability. This process helps create a uniform suspension of fibers called pulp.
b. Formation: The pulp is poured onto a moving mesh screen, known as the paper machine wire, which allows the water to drain while retaining the fibers in the desired pattern and thickness. The remaining water content is further removed using mechanical pressing and vacuum systems.
c. Drying: The wet paper sheet is then passed through heated rollers or a drying section to evaporate the remaining water and increase its strength.
Finishing:
a. Sizing: The paper may undergo sizing, a process where starch or other chemicals are applied to improve its surface properties, such as water resistance and printability.
b. Coating: Some types of paper, like glossy or coated paper, receive an additional coating layer to enhance smoothness, brightness, and ink absorption.
c. Calendering: The paper can be passed through a set of heated rollers, called a calender, to further enhance its smoothness, gloss, and thickness.
d. Cutting and Reeling: The large paper rolls are cut into smaller rolls or sheets of desired dimensions and then wrapped for storage or transportation.
It's important to note that there are variations in the paper manufacturing process depending on factors like the type of paper being produced (e.g., newsprint, fine paper, tissue paper) and the specific machinery and technologies used by different paper mills.
Visit: https://bestpaperaward.blogspot.com/
#PaperManufacturing
#PulpAndPaper
#PaperProduction
#SustainablePaper
#GreenPaper
#PaperIndustry
#Papermaking
#InnovationInPaper
#EfficientPaper
#RecycledPaper
Facebook: https://www.facebook.com/profile.phpid=100087106114908
Twitter : https://twitter.com/bestpaperaward
Pinterest : https://in.pinterest.com/bestpaperaward
Linkedin : https://www.linkedin.com/in/esha-gupta-18b2b4245
Linkedin : https://www.linkedin.com/in/esha-gupta-18b2b4245
Instagram: https://www.instagram.com/eshagupta__2022/
Comments
Post a Comment